High Rise Facades
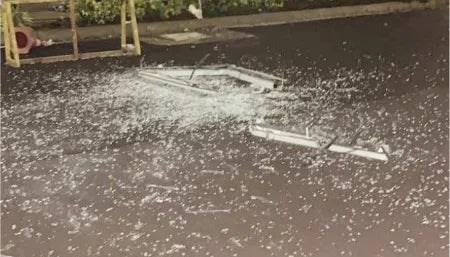
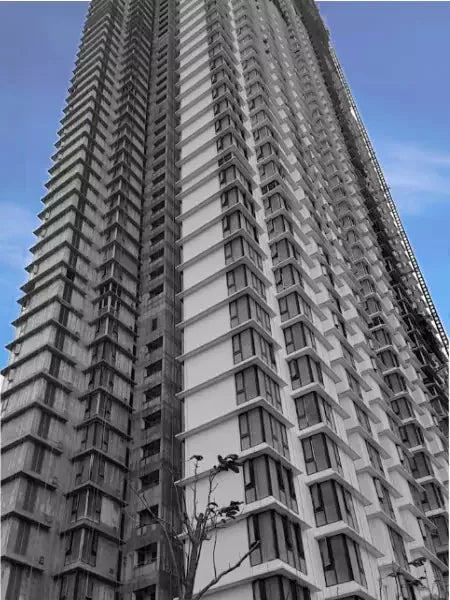
High Rise Facades
Generation demand for High rise buildings and high living luxury residentials developments has driven huge demand for new breed of building developments and New designs often have no precedents. We focus on residential high rise buildings which face unique challenges of many different types of openings as per user demands. For the last 10 years or so, high rise developments with multi-functional high rise facade requirements have posed great challenges. However the solutions for operable have not been able to tackle the fast faced requirements. This has resulted in less time to create new solutions and often designs used somewhere else are adopted.
Unfortunately we have been witnessing failures of operable in high rise facades which poses greater safety risks for both occupants and the public.
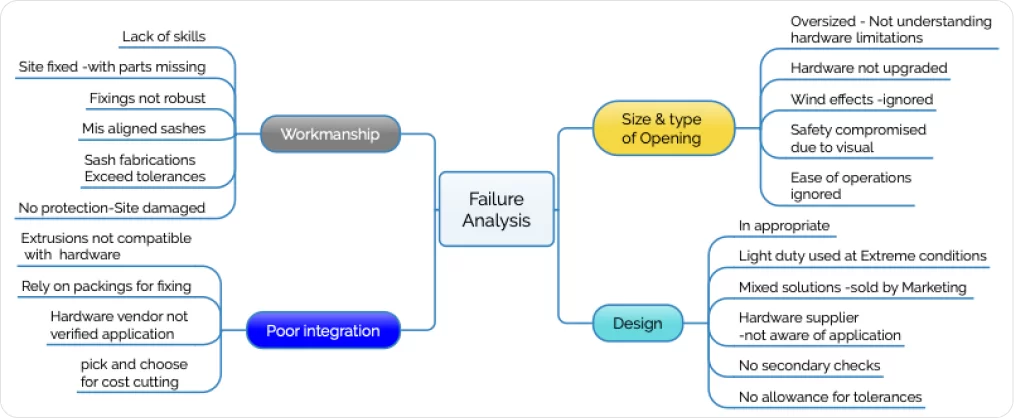
Failure Analysis
Big difference in hardware strength, ie,.test condition Vs actual site condition. Hence we can’t just check weight capacity alone. Reliability is non linearly reduced due to workmanship defects as explained in the graph/flowchart.
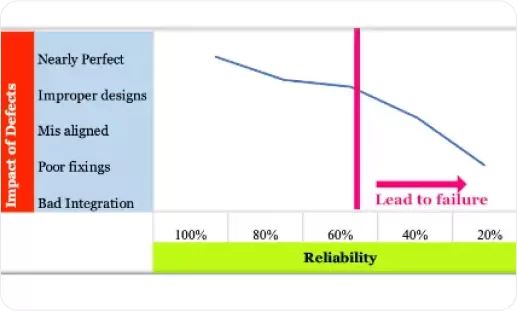
How is this done – Elsewhere
Many parts of Asian countries enjoy comfortable weather for considerable period of the year. Hence large openings, natural ventilations are key requirements of building facades. Other regions face extreme hot or Cold climates where in operable may not be key design features. For example in European region, high rise residentials generally have sealed envelopes with limited operable or ventilated facades. Our region requires new design solutions, hence imported design solutions from other regions may not work unless local challenges are well thought of.
Local Requirements
Requirements vary within regions, for example Singapore highrises (residential / commercial) do not require openings other than Fire Access Panels,. Whereas Indian building code (NBC) recommends 10% facades to have operable for smoke and fire evacuation purposes. Hence these provisions on high rise buildings which experience high wind pressures need robust operable hardware solutions. Designing openings in highrises requires good integration all the way from design to implementation. Often sizes and design requirements are not the same, hence every building requires skills and experiences to safely design the operable with the right hardware.
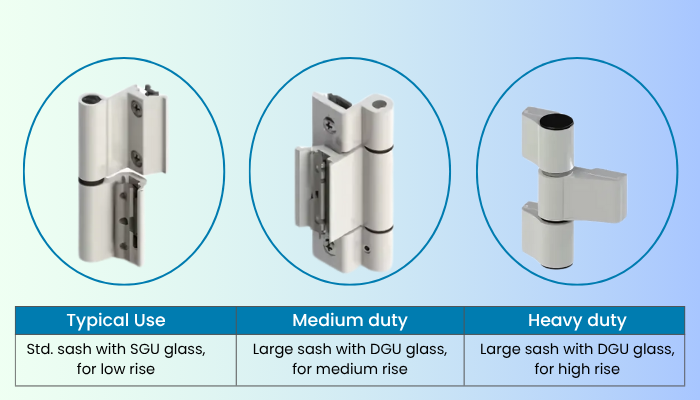
Comparison of typical Casement application
Just adding more light duty hinges in place of heavy duty hinges is NOT a safe solution. Heavy duty hinges have different fixing methods which reduces risk for challenging applications., Likewise whole range of components, not just a single component is to be given adequate attentions so that overall hardware system becomes reliable and safe.
Why should I bother ?
I am using the best International brand
Hardware is generally restricted to a handful of international brands which have good track records. However premium brands do not guarantee their designs for local challenges. Just relying on brand value alone may not be adequate to take care of design safety. We have witnessed several failures which have used premium branded hardware.
Unfortunately there is no one- stop solution for façade integrated operable, for example a brand who makes handle and locks does not necessarily have robust reliable stay arms. Therefore just relying on a supplier team, with their commercial interest to sell their own products may not be the right solution.
Due to these challenging requirements, pick and choose approach may work better with proper integration and assembly which may yield best of everything. However these require deeper involvement of façade designers, good experiences, deep integration techniques, co-ordinations, etc,.
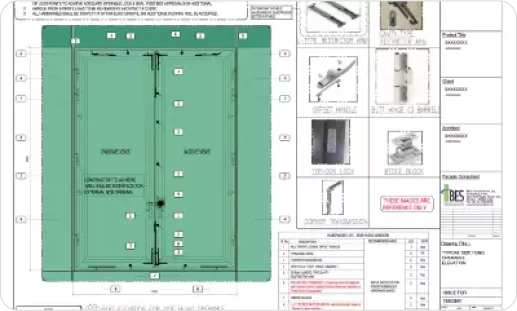
Some key aspects of high-rise facades hardware details are presented here as good design and implementation approach. Design and finalise hardware at the design stage rather than fabrication stage, will greatly reduce any risks. Sample of BES drawing of pre-construction stage shows hardware details.